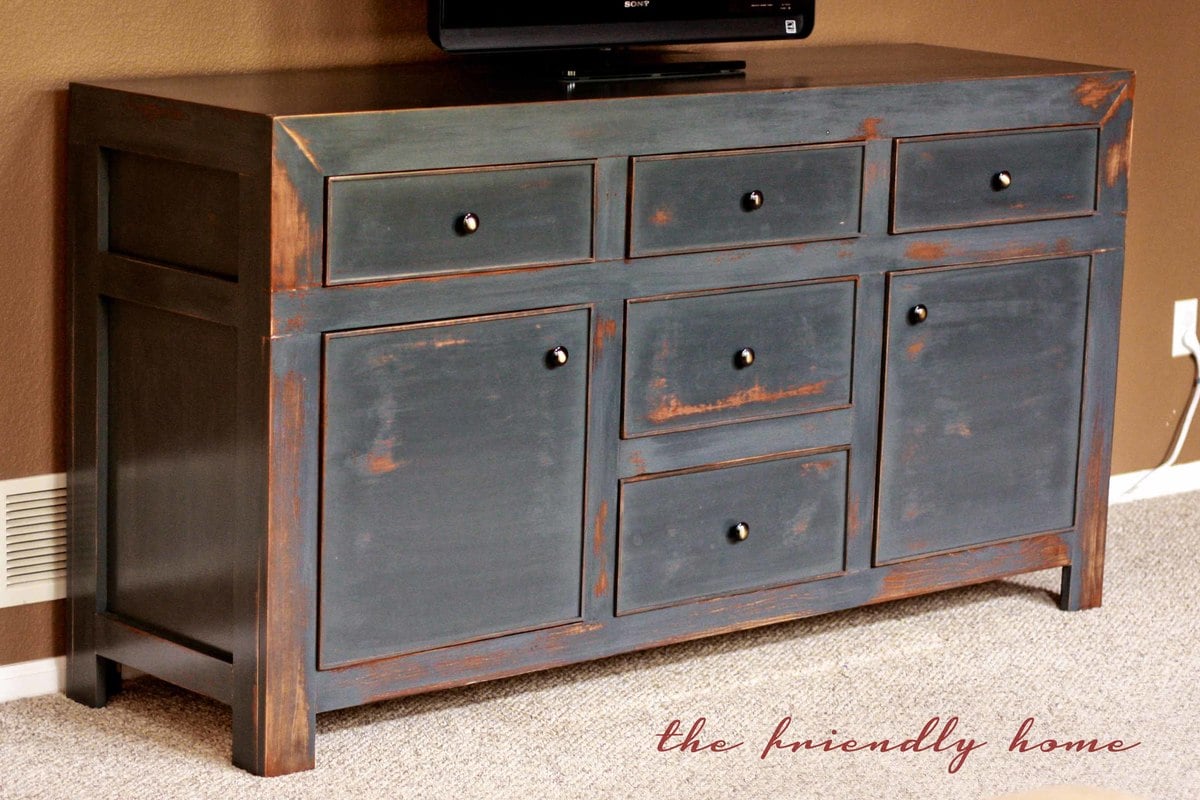
Free plans to build a media console inspired by Pottery Barn Dawson Media Console
Pin For Later!
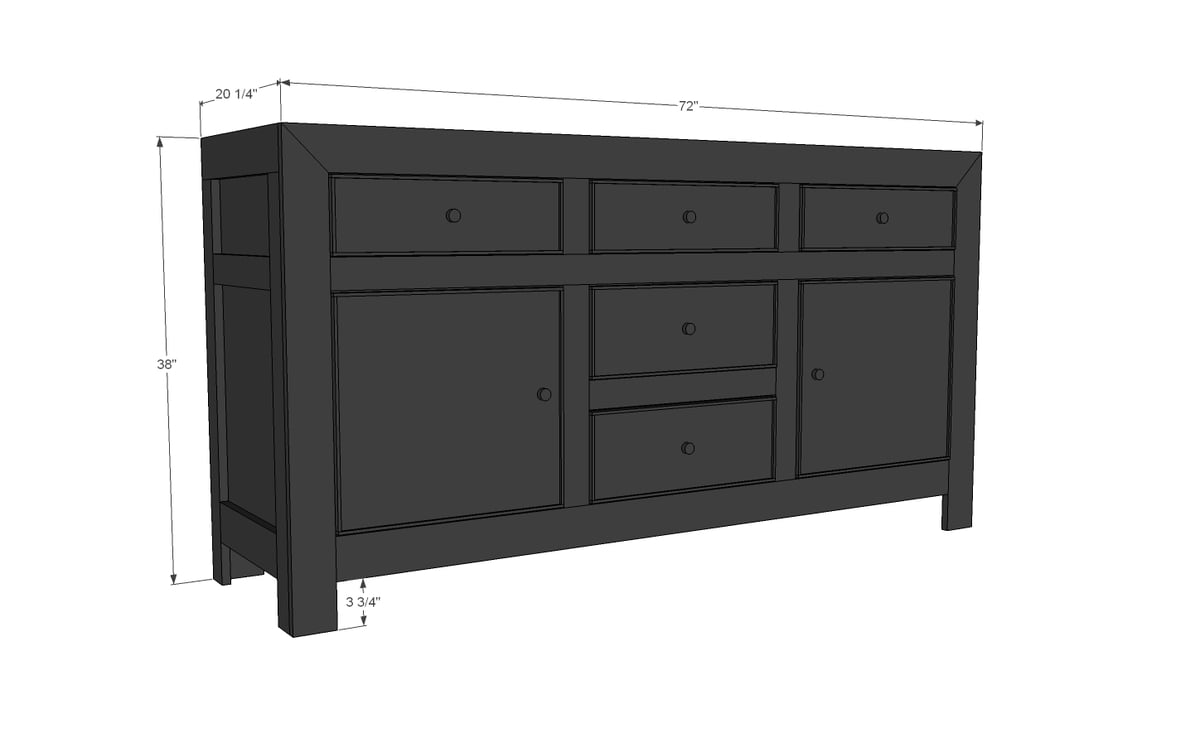
Preparation
- 2 - sheets 3/4” plywood ripped into strips 19 1/4” wide TIP: Use remaining strips for drawer box construction
- 1 - sheet 1/4” plywood for back and drawer bottoms
- 4 - 1x4 @ 8 feet long
- 3 - 1x3 @ 8 feet long
- 1 - 1x6 @ 6 feet long
- 1 - 1x8 @ 4 feet long
- 5 sets drawer slides (18” or shorter, two must be bottom mount or else you will need to add additional interior blocking)
- 2 sets hinges for inset doors
- Depending on drawer slides, drawers can be made to different widths. I have not accounted for the 1x6 and 1x4 boards needed to build the drawer boxes.
- 36 feet of 1/4" thick edge beading to frame doors/drawer faces
MAIN BOX
- 2 - 3/4” plywood @ 19 1/4” x 70 1/2” (top/bottom)
- 2 - 3/4” plywood @ 19 1/4” x 23 3/4” (shelves)
- 2 - 3/4” plywood @ 19 1/4” x 31 1/4” (dividers)
- 1 - 1/4” plywood @ 32 3/4” x 70 1/2”
SIDE FACE FRAMES
- 2 - 1x4 @ 19 1/2”
- 4 - 1x3 @ 34 1/2”
- 2 - 1x3 @ 14 1/2”
- 2 - 1x4 @ 14 1/2”
FRONT FACE FRAME
- 1 - 1x4 @ 72” (long point to long point, both ends cut NOT parallel at 45 degrees)
- 2 - 1x4 @ 38” (one end cut at 45 degrees, longest point measurement)
- 2 - 1x3 @ 6 1/4”
- 1 - 1x3 @ 65”
- 2 - 1x3 @ 18 1/2”
- 1 - 1X3 @ 20”
- 2 - 1x4 @ 5 1/4” (back legs)
DRAWER/DOOR FACES
- 2 - 3/4” Plywood @ 19 1/4” x 17 3/4”
- 3 - 1x6 @ 19 1/4”
- 2 - 1x8 @ 19 1/4”
- Edge beading is 1/4” thick, expected to frame all drawer faces
- Build three drawers to fit 20” wide openings from 1x4s (top drawers)
- Build two drawers to fit 20” wide openings from 1x6s
Please read through the entire plan and all comments before beginning this project. It is also advisable to review the Getting Started Section. Take all necessary precautions to build safely and smartly. Work on a clean level surface, free of imperfections or debris. Always use straight boards. Check for square after each step. Always predrill holes before attaching with screws. Use glue with finish nails for a stronger hold. Wipe excess glue off bare wood for stained projects, as dried glue will not take stain. Be safe, have fun, and ask for help if you need it. Good luck!
Instructions
Step 1
Step 2
Step 3
Step 4
Step 6
Step 7
For more details on how Hillary hung her doors - please stop over and visit Hillary here.
It is always recommended to apply a test coat on a hidden area or scrap piece to ensure color evenness and adhesion. Use primer or wood conditioner as needed.
Comments
Juanita_r
Wed, 06/05/2013 - 14:28
Amazing Ana & Hillary!!!!!
This is so incredibly beautiful!!! I absolutely love it. and the finish looks so cool. Amazing Ana & Hillary!!!
volador76
Wed, 06/05/2013 - 20:27
dawsen media console
wow! that's a beautiful piece of furniture!!! I have to make one but for some reason I can't download the plans can somebody help me?
JenWoodhouse.com
Thu, 06/06/2013 - 09:18
So impressed!
Omgosh! This is amazing! I love the build (can't believe plywood could look so good!!!) and the finish! You guys did a spectacular job!
HandsOnMike
Fri, 06/07/2013 - 09:32
Why do I get a Error when i
Why do I get a Error when i try to download the PDF?
PJM6379
Wed, 02/19/2014 - 19:31
Not Sure they Built this
Plans, or general directions Ana has given are incorrect, for instance the (4) vertical pieces (2) ends and (2) middle pieces that comprise the main body they have you only cutting (2) what are you to support the interior shelves on air? Very little detail and actual critical path planning and steps leads me to believe they did not build this in real work application. If you `follow the link to "her friend" you will notice the progression of the build, however the finished product looks like the pottery barn, I shouldn’t say looks like it is the pottery barn furniture refinished, notice the detail in the face frames...appears to a 1x4 using a flush trim router bit, however that would not work using the instructions they give, as the door would protrude and hit the stop before closing, the doors are not 3/4" in the picture, nor is the lathe they call depicted in the photo, the proportion and scale are off. A couple of questions that the people have asked raise questions as to the competence, for instance someone asked for clarification on the (4) 15/16” pieces, she drew a blank, however there was more detail in her husband not finding the material at home depot, and she and Ana went back and forth as to whither it would work or not, not to mention there are (7) drawer faces, that’s a ton of work just to simply blank on. It would be something entirely different had there been more than one component measuring 15/16” but they had to rip it down and it’s the only component repeated several times I find this very troubling. My wife has asked me to build several of these projects, the simple ones usually work, however the more complicated the item, the more problematic the plans are, I find myself using the plan as a starting point, then designing the project from there. My advice is to think the project through its entirety and question every step they give, as I have found there are better ways to do it making the piece, more structurally sound, better looking along with truer and squarer.